Is a 100% solids epoxy the right product for your job?
Is a 100% solids epoxy or urethane the right product for your job?
What about 100% solid coatings? It’s a question we’re getting from our customers fairly often these days. They’re currently quite the trendy product in industrial coatings technologies. While 100% solids epoxy and urethane coatings do provide some definite benefits, and are certainly a solid (sorry) solution in some scenarios, they’re not always the best solution. In some cases, equally effective (and less expensive) options exist. Here we’ll explain what they are, why they’re used and why they’re not an automatic pick as your best coating option.
100% solids epoxies explained
Before we dive into some of the benefits and drawbacks of 100% solids coatings, let’s define that term. What does the 100% refer to? By comparison, what would a 50% solid be?
When coatings are applied, two thickness measurements are taken. One is a wet film thickness (WFT) and the other is a dry film thickness (DFT). The paint is measured once before it has dried, and once again after.
The percent solid refers to the percentage of paint thickness that remains after the paint has finished drying, or the difference between the WFT and DFT. Usually, a percentage of the solid is lost and thickness is reduced during the drying process. To compensate, more coats are added until the desired thickness is achieved. For example, a 50% solid would require two coats at 20 mils of thickness to achieve a DFT of 20 mils, whereas a 100% solids epoxy would only require a single coat.
This is not the case with 100% solids. They are prized for maintaining the same level of thickness between the time they are applied and the time they have dried, hence the name 100% solids.
Zero VOCs and other benefits
For the reasons discussed above, 100% solids coatings require fewer coats to achieve the desired thickness level than other options. This is a big draw for facility owners and managers who request them most often. Fewer coats mean less chance of inter-coat adhesion problems and reduced time for the coating process, since there are no multi-step curing procedures in between coats.
Also, a 100% solids epoxy or urethane contains no volatile organic compounds (VOCs). Loss of thickness between WFT and DFT in lower solid coatings is due to the evaporation of solvents into the atmosphere as the coatings cure. These evaporating solvents (VOCs) can create dangerous environments in confined spaces and health hazards for workers. A lack of VOCs is often what makes 100% solids ideal for use as tank linings, or in shops were large numbers of coatings for railroad tank cars are applied.
Rapid drying times are another benefit of 100% solids. Often, drying times are so short that the coatings are sprayed from plural component systems, meaning the coatings are not mixed until the moment they are sprayed from the gun. They can then be walked over in a matter of hours. Reduced downtime and quick project turnarounds have serious appeal for owners who need their equipment back in service fast. In some cases, service tanks are back in use in a matter of hours rather than days.
Additionally, there is the option to add fiber to many of these high solids coating formulations. This provides some additional support for structures getting on in their years. For projects like storage tanks, a 100% solids epoxy or urethane can actively contribute to a longer life span.
Not a no-brainer
As mentioned earlier, 100% solids are not a coatings cure-all. They have some definite benefits, including the ones discussed above. But the sheer range of coatings options available makes it unwise to latch onto one option before exploring others.
Often it is the case that a few more coats of paint will not exceed the price of buying a more expensive product in the first place. In these scenarios, owners may be better served by choosing a product with properties that are known to suit the needs of their environment, instead of focusing on the percent solids.
In other situations, a little extra drying time won’t make or break an owner’s schedule. If a scheduled maintenance period already exists, or factors other than drying time are keeping your equipment out of service, rapid drying times may not necessarily do you any good.
And as always, even with the best coatings products on the market, poor surface preparation can ruin a job just as quickly as our 100% solids epoxies dry. Skimping on surface prep will shorten the life of your coatings system, guaranteed. Choosing a product without a proper quality control and quality assurance plan for the life of the coatings system will also threaten its effectiveness.
A 100% solid epoxy or urethane may be the best option for your project. It depends on a number of factors. Before you choose, get in touch with US Coatings to discuss your project with a qualified coatings representative. We’ll talk you through the entire process, from product selection and surface preparation to application and equipment recommendations.
For our entire list of 100% solids and low VOC coatings, click here to view our full product catalog.
For our specific epoxy primers and finishes, see our epoxy product page.
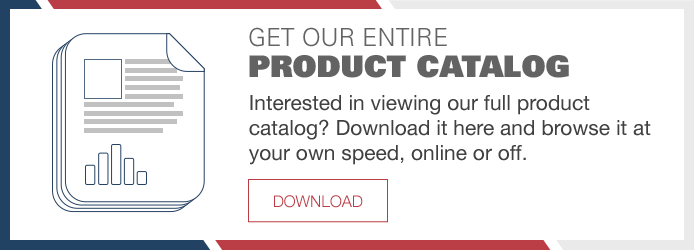